The Yarn You've Been Waiting For
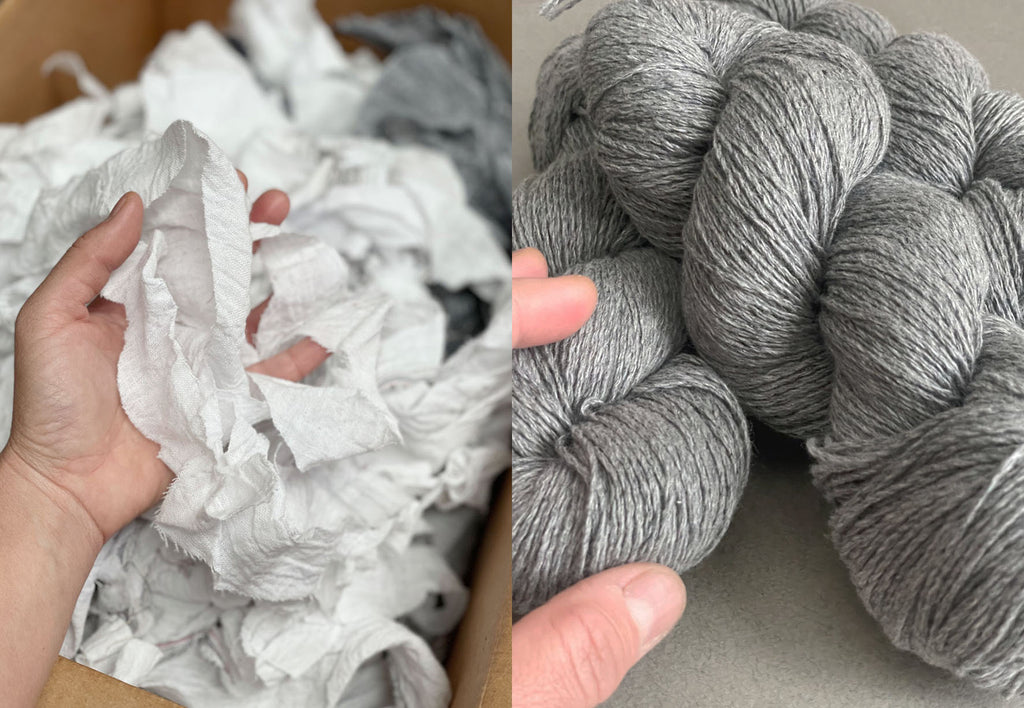
We can’t tell you how long we’ve been waiting, and searching for this. Our studio heaves under the weight of textile cuttings (formerly known as offcuts, waste, scraps).
For years we’ve been storing it all to avoid landfill, but we also saw this excellent waste material as a resource. They are cuttings after all, ready for propagation.
Jumping in.
Despite the many challenges we were facing with Covid at the time, we started our recycled yarn research process and met with Guy from Dempstah via FaceTime. How do we do this?
We couldn’t believe what we were learning.
Guy was working with an incredible facility based in Hong Kong that could turn textile waste fibres into new yarn without any water, dye, bleach, detergent, liquid chemicals or anything.
Get this.
The existing hues from our textile cuttings would be blended to create new, unique recycled yarn colours - without bleaching or dyeing. For real. This was way more sustainably awesome than we could have ever dreamed!

First things first.
We needed to see if our cuttings would cut the mustard. Can they be recycled into high quality yarn for industrial knitting and weaving?
Guy was about to send a shipment to the mill so we could tag on our sample batch as part of this consignment.
We realised we were best to separate the cuttings by colour and fibre type. These would be the individual ingredients in Guy’s recipe to cook up the final coloured yarn. So we dug into a part of our stash, re-sorted and prepared about 30kg of cuttings for the first test run. We were buzzing with excitement!
This happened in June 2021.
Because we had a high proportion of linen cuttings, Guy proposed that we try to create a 6ply / sport-weight yarn for knitting summer-weight items. The higher linen fibre content would create an exquisitely dry but soft yarn with a slightly crisp handle and weighty drape.
Getting somewhere.
A few months on, the mill got back to us after a bunch of trials. They had sanitised and finely shredded our textile cuttings into fleece. The cotton / linen blend fabric cuttings were easy to work with. However, the 100% linen fibres were troublesome due to their innate dryness and brittleness.
Guy suggested that we blend with silk or wool to bolster the fibres and strengthen the spin. From his experience, the final yarn of approximately 50% recycled fibre and 50% virgin fibre created an optimum, unique quality. The question was - what was the best virgin fibres to blend with the recovered fibres, and in what proportions?
Guy proposed a beautiful finished yarn could be 50% recycled fibre, 40% organic cotton,10% silk. Sounded good to us. We had many more questions. You can imagine.
Wait.
There was a long period of not hearing from Guy or the mill. And when we finally did, the news was a little discouraging.
In the combing stage, they discovered that our 100% linen fibres had a 36% fibre loss which was not very good at all. From 100kg, we would only get 64kg of spinnable fibre. However, the fibre loss on the cotton / linen was only 8%. From 100kg, we would get about 92kg of spinnable fibre which was amazing.
The mill decided to do one last trial of processing both 100% linen and cotton / linen fibre types at the same time to see what the loss and yield rate would be. This test aimed to capture the shorter linen fibres that may otherwise be lost in the general spread of fibres, and provide a better overall yield.
The time it takes.
We got to this point in September 2021, and didn’t hear from them again until November.
By this stage, we were feeling pretty anxious that we may have to go back and re-write this experimental recipe from scratch. But Guy was the bearer of interesting and wonderful news.
Working with so much linen was quite a new thing for the mill. Also, the fibre blend with organic cotton and silk didn’t feel quite right so they went ahead and experimented on the fibre blend - changing it to 50% recycled Mrs Woo fibre, 20% organic cotton and 30% wool.
They found that adding some fine wool rather than silk proved a lot more effective at capturing the short linen fibres in the spin, also improving yield rate to create the highest quality yarn. With Guy’s expertise in yarn development, he put forward the change from 6ply to 4ply and the mill to progress to spinning stage with the new fibre blend.
The lead time to make this yarn dream come true was estimated at about 2 months. Shipping time, 3-4 months. Not accounting for further Covid delays to production and shipping.
If we could eat it.
It was December 2021 when we received our very first sample cake of yarn. We couldn’t believe what we had in our hands! The resulting colour was a beautiful tarnished silver with the finest speckling of grey blue hues to give it an extra dimensional quality. It felt soft like light cotton wool with a supple, velvety handle.
It was completely dreamy.
We did it. Thanks to Guy and his dedicated work in this field, we propagated our precious textile cuttings into this exquisitely unique yarn.
And the best news from the mill was that they were willing to sell back what they had been able to produce with our sample batch. For real? This was just a test process! Guy and the mill were really pleased with the resulting yarn.
How could we say no?
We decided to go for it, despite the high sampling cost.
One more thing.
We finally received the shipment of completed yarn in June 2022. But Guy discovered that the spun yarn was a little too loose for his liking. He got in touch with Fibre Arts Shed in the Central Coast NSW to resolve this by putting the yarn through an extra spinning process to tighten the ply.
In the 18-month period of this process, we experienced a huge increase in production, international shipping and customs costs, plus additional unexpected processes. All this before adding the costs to prepare the yarn for us to use.
Let’s just say, this is an investment into the future.
It’s a long story, but this is just the beginning.
It’s September 2022 now, the start of Spring here. It feels timely that we’re heading into planting season. Our cuttings have been propagated for new textiles to grow.
Every garden needs tending, so time will tell how these yarns will eventually turn into textiles and clothing. We’re deep-diving into some intense learning right now on how to create 3D knitted garments. What’s that, you ask? With this yarn? Perhaps.
But for now.
We can have these beautiful cakes of yarn, and eat it too.